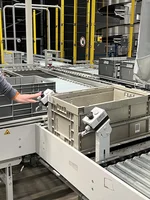
Strategic solution for warehouse management
SAP EWM is the strategic solution for SAP warehouse management. SAP LES and SAP WM have reached the end of their life cycle and will soon no longer be maintained by SAP.
New features and functions for warehouse management are already being developed by SAP exclusively for SAP EWM. SAP EWM has been integrated into SAP S/4HANA (Embedded EWM) since S/4HANA 1909. Since then, the integration between SAP EWM and SAP MM and SAP SD directly in S/4HANA has been driven forward.
As an alternative for existing warehouses, the SAP Stock Room Management module was introduced as a simple warehouse management solution with the basic functions from SAP WM. However, no new functions will be implemented here either.
If you manage your warehouses with SAP WM or SAP LES and want to continue to benefit from the advantages of optimal interaction between your logistics components and new warehouse management functions in the future, it may be worth switching to SAP EWM. However, it does not always make sense to switch immediately. If you would like to evaluate which strategy makes the most sense for your company or find out more about the various warehouse management systems from SAP, please get in touch with us.
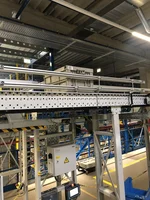
What is SAP Extended Warehouse Management?
- SAP EWM enables you to automate the control of warehouses of all sizes
- Fully integrated solution for warehouse management
- Management of stock levels in storage bins, vehicles and resources in the warehouse
- Control of complex processes - from goods receipt to internal processes such as replenishment, inventory and additional logistics services through to goods issue
- Mapping, tracking and documentation of movements in the warehouse
- Flexible warehouse structures
Learn more: SAP EWM SAP EWM Assessment
SAP Extended Warehouse Management
An excerpt from the range of SAP EWM services
SAP Extended Warehouse Management (SAP EWM) is a modern warehouse management system from SAP. SAP EWM enables you to efficiently manage your inventories in warehouses of any size and complexity, as well as to control, execute and track all warehouse logistics processes.
SAP EWM is SAP's strategic solution for warehouse management.
-
Storage bin and stock management
SAP EWM enables the optimal placement of products in the warehouse - depending, for example, on the nature of the products and the frequency of access - with permanent inventory transparency at the same time.
-
Mapping of goods movements
With SAP EWM you achieve full transparency of your warehouse movements as well as the optimization of warehouse capacities and material flows in all warehouse and intralogistics processes. The entire goods and process flow may be traced transparently at any time.
-
Planning and monitoring
Plan your flow of goods from incoming goods through production supply to shipping. With the warehouse management monitor you always have an overview of your material and process flows.
-
Work scheduling and resource management
With the integrated documents you can optimally plan and monitor your workload in the warehouse. Based on the workload, the resource management of SAP EWM offers you the possibility of utilizing your staff, their areas of responsibility and your technical resources optimally.
-
Mobile devices
SAP EWM enables paperless processes through the integration of mobile devices in all warehouse logistics processes. The wireless data connection gives you a real-time overview of your material and process flows in the warehouse.
-
Warehouse control and automation
With the integrated material flow control (MFS), SAP EWM offers you an integrated, standardized interface to automatic warehouses and conveyor systems without the use of an additional warehouse control computer. If necessary, MFS communicates directly with the PLC.
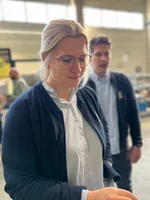
Transition from SAP WM to SAP EWM
SAP has currently (as of 12/2020) scheduled the end of SAP Warehouse Management for the end of 2025. Therefore, many SAP users are already looking for an alternative for their warehouse management.
The new strategic solution of SAP for the warehouse management is SAP Extended Warehouse Management.
However, the migration to SAP EWM from SAP WM must be carefully considered. Many companies have invested heavily in their logistics processes over the years. This includes customer-specific developments in SAP WM and the corresponding customizing. Some of the customizing may be migrated from SAP WM to EWM. Developments in SAP ABAP usually have to be re-implemented in SAP EWM since the technical environment differs greatly.
For small warehouses in particular, you should therefore consider using SAP Stock Room Management in SAP S/4HANA. SAP Stock Room Management contains the basic functions from SAP WM and should remain a permanent part of SAP S/4HANA. The decision about the right warehouse management system in SAP S/4HANA is as individual as your company itself.
The following advantages favor a migration from SAP WM to SAP EWM:
- Consistent process support from incoming goods to dispatch
- The best possible transparency of your inventory and processes
- Automation of processes and resources possible
- Connection of your automatic warehouse without an additional warehouse control computer
- Paperless processes through mobile end devices connection "out of the box"
- Complete integration in S/4HANA and other SAP solutions
- Maintenance and advance development by SAP
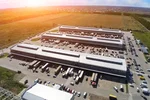
SAP EWM - Overview of the range of functions
Goods Receipt
The goods receipt in EWM begins either with an advised delivery or with an expected goods receipt based on a purchase order. In each case, however, an inbound delivery is created in EWM, which serves as the basis for goods receipt processing in EWM.
The process for goods receipt processing can be customized in EWM according to your requirements. Several different goods receipt processes are also possible, e.g. depending on the supplier or material.
One type of goods receipt processing is described below:
Goods receipt posting
With the goods receipt posting, you confirm the physical arrival of the goods in your warehouse.
Unloading
During unloading, you move the delivered pallets from the truck to your goods receipt area.
Deconsolidation
During deconsolidation, you can repack the delivered pallets onto suitable storage pallets, for example, so that the goods are suitable for your individual warehouse.
Quality inspection
In the quality inspection step, you check the quality of the delivered goods. The quality check can be carried out in different ways.
Putaway
In the putaway step, the system uses a configurable putaway strategy to determine the most suitable storage location for the material for final putaway. The goods receipt process is then completed and the goods are available for retrieval.Der Wareneingang im EWM beginnt entweder mit einer avisierten Lieferung oder mit einem erwarteten Wareneingang auf Basis einer Bestellung. In Jedem Fall aber wird im EWM eine Anlieferung angelegt, die als Basis für die Wareneingangsbearbeitung im EWM dient.
Goods Issues
The goods issue process in EWM begins with an outbound delivery that is created either in the connected ERP or S/4HANA system, on the basis of a sales order or as an unplanned withdrawal, e.g. to a cost center, or directly in EWM (direct outbound delivery).
Different, freely configurable goods issue processes can be found in EWM based on the outbound deliveries.
An example of a goods issue process is described below.
Transportation planning
You have the option of carrying out transportation planning in EWM. This allows you to plan which deliveries are to be dispatched together and when they are to be dispatched. However, transportation planning can also be carried out in a connected transportation planning system or in ERP or S/4HANA and transferred to EWM.
Wave management
You can combine the picking of several outbound deliveries into so-called waves. This makes it possible to bundle similar outbound delivery items and carry out workload planning. When the waves are released, the warehouse tasks for picking are created and bundled into work packages.
Picking
During picking, the materials requested for delivery are picked from the warehouse for dispatch. Picking can be carried out in different ways. Further information on this can be found in the Picking section.
Packing
In this process step, you pack the picked goods in suitable shipping containers and print the shipping documents that you need to attach to the package. The documents can be printed directly from EWM.
Staging
In the staging step, the shipping containers and pallets are prepared for loading in the staging zone. The staging zone is usually an area in front of a gate. The correct staging zone is determined via the process or via the gate assignment of the transport unit.
Loading and goods issue
Once the goods have been prepared and staged for shipping, the shipping containers and pallets can be loaded. After loading, the goods issue process is completed with the goods issue posting for EWM and the goods are posted from stock in the system.
Production supply
With SAP EWM, you can transparently map the entire production supply process from material requisition, staging, material consumption, clearing of the production supply area to goods receipt processing of the manufactured material.
There are two different technologies for material staging: staging via deliveries and staging via production material requirements.
With delivery-based staging, you create an outbound delivery for the components of your production order. Based on the delivery, the materials are picked, staged and booked out of the warehouse system stock with the goods issue posting. It is possible to consume the stock in the system directly against the production order or to transfer the stock to a non-EWM-managed storage location and then consume it directly in the connected ERP or production system.
When staging via the production material requisition (PMA), a PMA document is generated in EWM on the basis of the production order, on the basis of which the staging and material consumption is controlled. The advantage of using the PMA document for production supply is that partial requests for components can also be made, e.g. for a procedure, and components can be requested again, e.g. in the event of unplanned excess consumption.
The components can be provided in three different ways with the PMA document:
Order-specific
With order-specific staging, you only request the components for one production order. The order-specific staged stock can also only be used for one production order.
Cross-order
With cross-order staging, you can stage a material that is required for several production orders. The staged material has no direct document reference and can therefore be used for all production orders.
No provisioning
With this provisioning method, there is no physical provisioning. The stock for the required components is always stored in sufficient quantities in a storage location in production and is consumed directly from there. To ensure sufficient stock, you can use an automated replenishment process or a Kanban process, for example.
You can define the type of provision for each component in a PMA document. This makes it possible to combine the staging methods.
Internal processes
All processes that are required exclusively for the internal operation of a warehouse are summarized under the generic term internal processes. The most important internal processes in SAP EWM are briefly explained below.
Replenishment
With the replenishment process, you ensure that materials are always available in sufficient quantities in the required storage bin by replenishing them from your reserve area.
In EWM, a distinction is made between planned and unplanned replenishment. With planned replenishment, for example, you can always ensure that the materials are stored in sufficient quantities in your quickly accessible storage bins before starting picking for outbound deliveries and production orders. You can carry out planned replenishment based on the workload planned in the system or the stock situation, for example. Unplanned replenishment is always triggered by the system if the stock of a material on a shelf or in a storage bin falls below a definable threshold value when it is removed from storage.
Inventory
SAP EWM offers you a transparent way of planning and executing the inventory of your stock. You can choose between storage bin-based and product-based stocktaking. EWM also offers various inventory procedures such as stock-in and stock-out inventory (low stock inventory), ad hoc inventory, cycle counting and an interface for inventory sampling. You can combine the inventory procedures as you wish in order to select the most suitable solution for you. The inventory process can be fully integrated into the radio data link or paper-based.
Scrapping
With EWM, you can map your scrapping processes in the warehouse. Whether breakage or planned activities, such as checking the shelf life of your stock. You can freely define the scrapping process, regardless of whether you want to book out the stock directly in the storage bin or move it to a scrapping zone first.
Additional logistical services
With EWM, you can map additional logistics services (value-added services), i.e. value-adding activities in your warehouse. Such value-adding activities can be simple assembly work, the separation and packing of articles or the creation of kits from several components to form a header product.
EWM provides a separate document for such activities, which contains the work instructions and which you can use to post the material transfers or consumption of auxiliary products such as packaging, oils, etc.
Additional logistics services can be integrated into the goods receipt and goods issue process in EWM or carried out as an independent process.
Storage control
Warehouse management in SAP EWM is a powerful tool for controlling processes and goods movements in your warehouse. With process-oriented and layout-oriented warehouse control, SAP offers you two different but combinable options for process definition.
Process-oriented storage control
With process-oriented storage control, processes are defined with individual process steps. Each process step can be assigned its own target location. When a process step is completed, the storage tasks for the target bin of the next process step can be created automatically.
Layout-oriented storage control
Layout-oriented storage control is used to map the physical conditions of your warehouse, e.g. identification and picking points, transfer areas or other broken transports. If a sink B can only be reached from a source A via a transfer point C, the transport can be mapped as three individual transports A - C - B.
Order picking
- Single-order picking
- Multi-Order Picking
- Combined Picking
- Pick and pack
- Pick and pass
- 2-stage picking
Resource management
- Resource management
- Task management using queues
Yard Management
Cross Docking
Serial number handling
Batch management
Batch management in SAP EWM enables the traceability of stock across the entire intralogistics process chain.
The batch obligation and the characteristics of the batch features are master data that are transferred from SAP ERP or SAP S/4HANA to EWM.
Catch Weight
SAP EWM supports catch weight for products that you need to manage in different units of measure, e.g. pieces and kilograms.
This is a fundamental requirement, particularly in the food sector and food retail and other areas where items are managed logistically in pieces but sold to customers in units of weight.
Handling Units
A handling unit is a load carrier (e.g. pallet) with the goods it contains. SAP EWM offers you the option of flexibly managing single or multi-level handling units and the stocks packed in them. Handling units have a unique identification and - if necessary - further identifications. The identification can be assigned externally (e.g. for permanently labeled containers) or internally and facilitates, among other things, the handling of logistics processes using mobile data applications.
Handling units in EWM do not require handling unit management to be activated in ERP or SAP S/4HANA for the respective storage location.